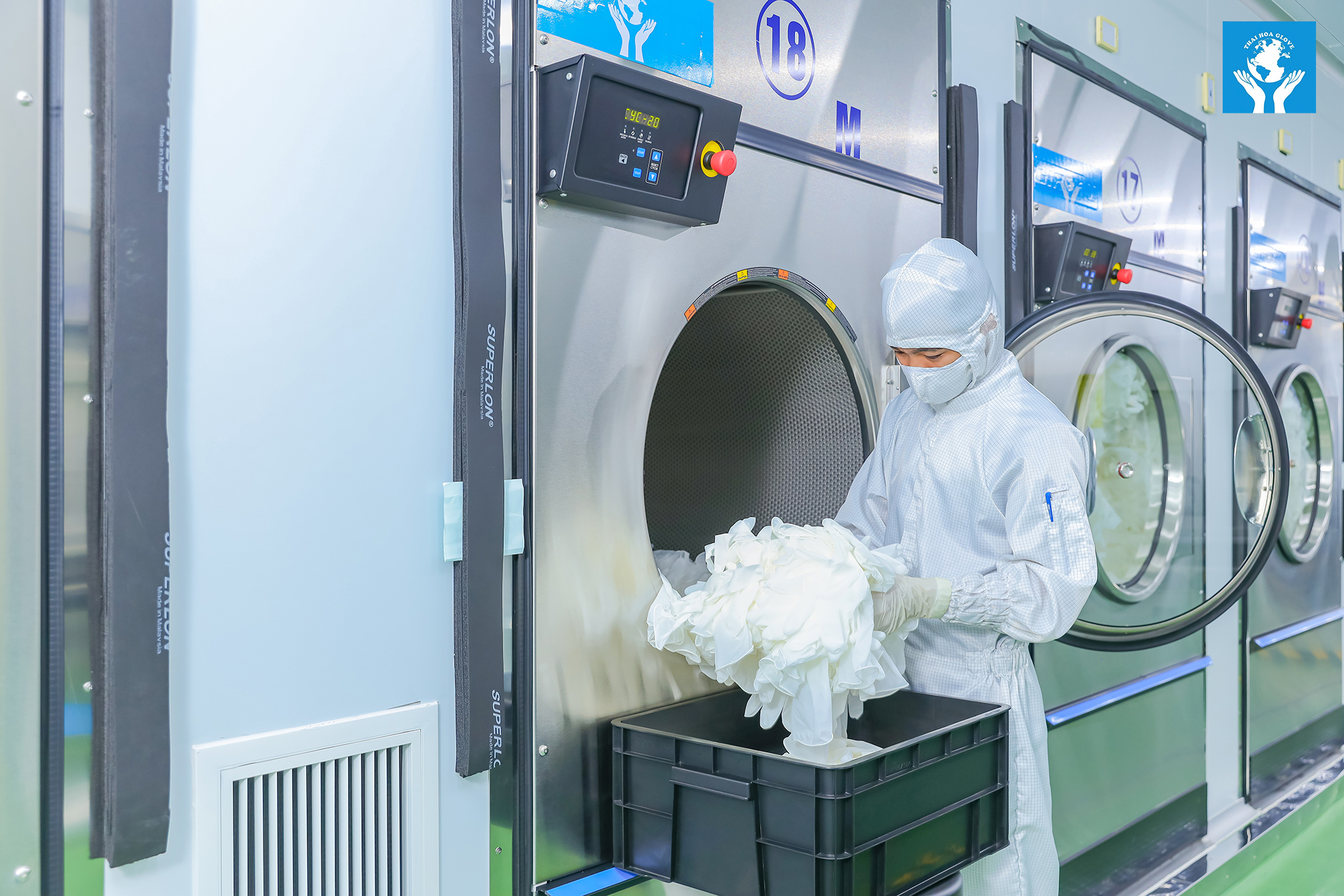
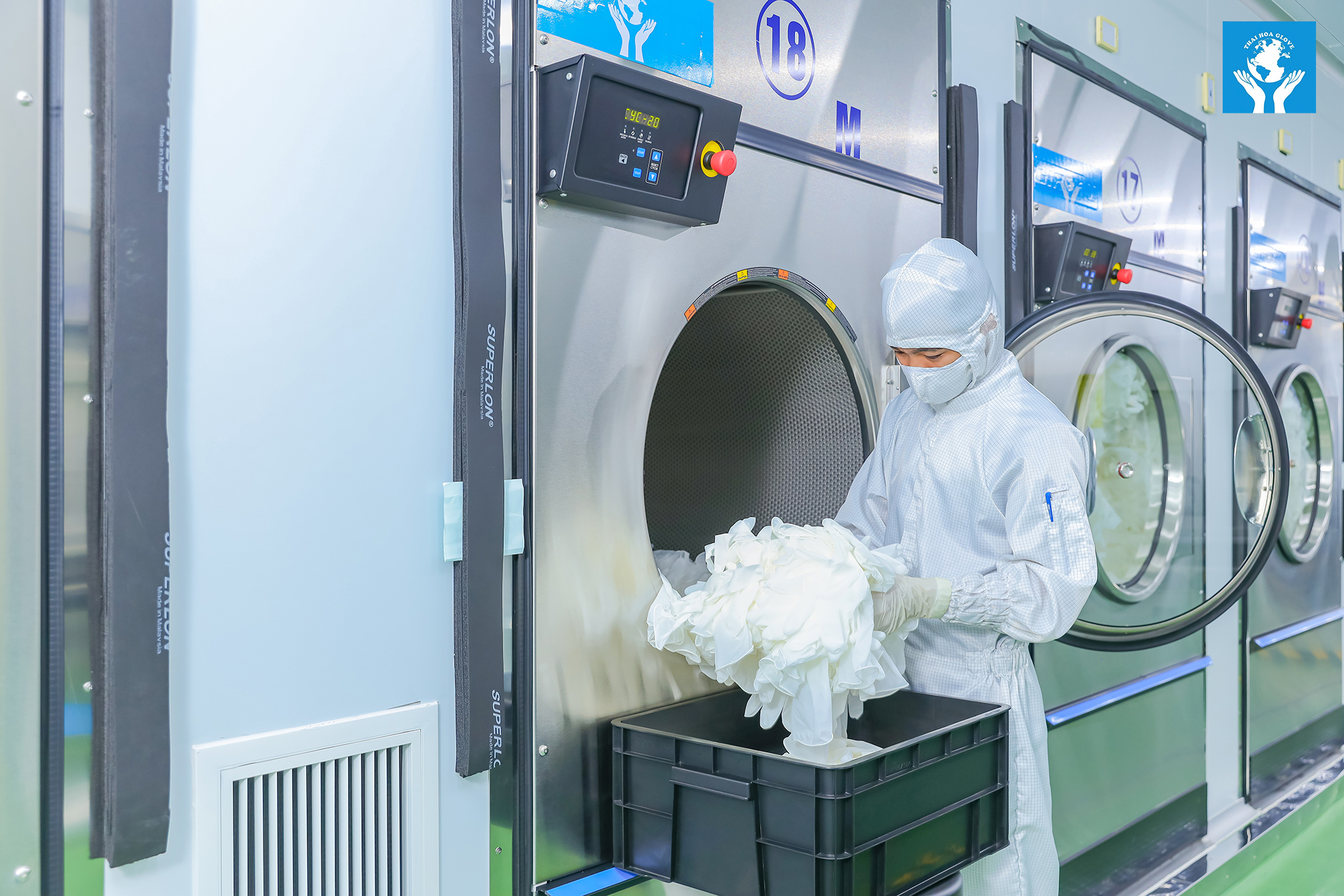
Phân Xưởng Xử Lý Sau Lưu Hóa: Hoàn Thiện Chất Lượng và Độ Sạch Găng Tay Phòng Sạch
Sau giai đoạn tạo hình và lưu hóa, găng tay bán thành phẩm vẫn còn chứa các tạp chất, dư lượng hóa chất… có thể ảnh hưởng đến chất lượng và độ sạch cần thiết cho môi trường phòng sạch. Phân xưởng xử lý sau lưu hóa đóng vai trò then chốt trong việc loại bỏ các tạp chất này, đồng thời thực hiện các công đoạn xử lý bề mặt đặc biệt (nếu có) để hoàn thiện sản phẩm trước khi chuyển sang giai đoạn kiểm tra cuối cùng và đóng gói. Đây là một phân xưởng quan trọng, đòi hỏi quy trình nghiêm ngặt và hệ thống kiểm soát chất lượng chặt chẽ để đảm bảo găng tay đáp ứng các tiêu chuẩn khắt khe nhất của ngành công nghiệp phòng sạch.
- Giặt và Làm Sạch Găng Tay:
Công đoạn đầu tiên và quan trọng nhất trong phân xưởng xử lý sau lưu hóa là giặt và làm sạch găng tay. Mục tiêu chính của quá trình này là loại bỏ:
- Dư lượng hóa chất: Các hóa chất còn sót lại từ quá trình lưu hóa hoặc các công đoạn xử lý trước đó.
- Tạp chất bề mặt: Bụi bẩn, các hạt polyme thừa hoặc các tạp chất khác có thể bám trên bề mặt găng tay trong quá trình sản xuất.
- Ion: Các ion kim loại có thể gây ảnh hưởng đến các quy trình nhạy cảm trong môi trường phòng sạch (ví dụ: sản xuất điện tử).
Quá trình giặt và làm sạch thường được thực hiện qua nhiều giai đoạn với các loại dung dịch và phương pháp khác nhau:
- Giặt sơ bộ: Sử dụng nước sạch hoặc dung dịch tẩy rửa nhẹ để loại bỏ các tạp chất lớn và bột dư thừa ban đầu.
- Giặt bằng dung dịch hóa chất: Sử dụng các dung dịch hóa chất chuyên dụng để loại bỏ các ion và dư lượng hóa chất khác. Nồng độ, nhiệt độ và thời gian rửa được kiểm soát chặt chẽ.
- Giặt bằng nước DI: Găng tay được rửa kỹ lưỡng bằng nước DI (nước khử ion) nhiều lần để đảm bảo loại bỏ hoàn toàn các hóa chất tẩy rửa và các ion kim loại. Chất lượng nước DI phải được kiểm tra thường xuyên để đảm bảo độ tinh khiết.
- Sấy khô: Sau khi rửa, găng tay được sấy khô hoàn toàn bằng hệ thống sấy khí nóng hoặc các phương pháp sấy khô khác trong môi trường kiểm soát để tránh tái nhiễm bẩn. Nhiệt độ và thời gian sấy được điều chỉnh để không làm ảnh hưởng đến chất lượng găng tay.
Hệ thống rửa và làm sạch được thiết kế tự động hóa với các băng tải và bể chứa liên tục, đảm bảo hiệu suất và tính đồng nhất trong quá trình xử lý.
- Xử Lý Bề Mặt Đặc Biệt (Tùy Chọn):
Tùy thuộc vào yêu cầu cụ thể của sản phẩm và ứng dụng, găng tay có thể trải qua các công đoạn xử lý bề mặt đặc biệt sau khi giặt và làm sạch:
- Clo hóa (Chlorination): Xử lý bề mặt găng tay bằng clo giúp giảm độ dính, làm cho găng tay dễ dàng đeo và tháo hơn, đồng thời giảm hàm lượng protein đối với găng tay latex, giảm nguy cơ gây dị ứng. Quá trình clo hóa cần được kiểm soát chặt chẽ về nồng độ clo, thời gian xử lý và sau đó phải được trung hòa và giặt sạch clo dư.
- Phủ Polymer (Polymer Coating): Phủ một lớp polymer mỏng lên bề mặt bên trong của găng tay (ví dụ: polyurethane) giúp găng tay trơn hơn, dễ đeo hơn và có thể cải thiện khả năng chống hóa chất. Quá trình phủ polymer đòi hỏi sự kiểm soát chính xác về độ dày lớp phủ và quá trình sấy khô sau đó.
- Xử lý chống tĩnh điện (Anti-static Treatment): Đối với các ứng dụng trong ngành điện tử, găng tay cần có khả năng chống tĩnh điện để bảo vệ các linh kiện nhạy cảm. Quá trình xử lý này có thể bao gồm việc nhúng găng tay vào dung dịch chứa chất chống tĩnh điện hoặc tích hợp chất chống tĩnh điện vào thành phần polyme ban đầu.
- Tạo nhám bề mặt (Texturing): Để tăng độ bám dính khi cầm nắm các vật dụng, bề mặt găng tay có thể được tạo nhám.
Các công đoạn xử lý bề mặt này phải được thực hiện trong môi trường kiểm soát để tránh nhiễm bẩn và đảm bảo tính đồng nhất của sản phẩm.
- Kiểm Tra Chất Lượng Sau Xử Lý:
Sau khi hoàn tất quá trình rửa, làm sạch và xử lý bề mặt (nếu có), găng tay sẽ trải qua một bước kiểm tra chất lượng nghiêm ngặt hơn, tập trung vào các yếu tố liên quan đến hiệu quả của quá trình xử lý sau lưu hóa:
- Kiểm tra độ sạch: Đo lường hàm lượng hạt bụi (particle count), hàm lượng chất không bay hơi (Non-Volatile Residue – NVR) và hàm lượng ion trên bề mặt găng tay để đảm bảo đáp ứng các tiêu chuẩn phòng sạch cụ thể (ví dụ: ISO Class). Việc kiểm tra này thường được thực hiện trong phòng sạch bằng các thiết bị chuyên dụng.
- Kiểm tra dư lượng hóa chất: Phân tích để đảm bảo không còn dư lượng hóa chất vượt quá mức cho phép sau quá trình rửa và làm sạch.
- Kiểm tra các đặc tính bề mặt: Đánh giá hiệu quả của quá trình clo hóa, phủ polymer hoặc xử lý chống tĩnh điện (ví dụ: đo điện trở bề mặt).
- Kiểm tra ngoại quan: Lặp lại việc kiểm tra hình dạng, kích thước và các khuyết tật bề mặt một lần nữa để đảm bảo không có hư hỏng phát sinh trong quá trình xử lý sau lưu hóa.
Các găng tay không đạt yêu cầu sẽ bị loại bỏ.
- Sắp Xếp và Chuyển Giao:
Những chiếc găng tay đạt tiêu chuẩn sau quá trình kiểm tra sẽ được sắp xếp theo lô, kích cỡ và các yêu cầu khác của khách hàng. Sau đó, chúng sẽ được chuyển giao sang phân xưởng kiểm tra chất lượng cuối cùng và đóng gói.
Kết luận:
Phân xưởng xử lý sau lưu hóa đóng vai trò then chốt trong việc đảm bảo chất lượng và độ sạch của găng tay phòng sạch. Các công đoạn giặt, làm sạch và xử lý bề mặt (nếu có) tại phân xưởng này loại bỏ các tạp chất và hoàn thiện các đặc tính cần thiết của sản phẩm. Quy trình nghiêm ngặt, hệ thống kiểm soát chất lượng chặt chẽ và việc tuân thủ các tiêu chuẩn về môi trường và an toàn lao động tại phân xưởng này là yếu tố then chốt để cung cấp ra thị trường những chiếc găng tay phòng sạch đáp ứng các yêu cầu khắt khe nhất, bảo vệ hiệu quả cho các quy trình sản xuất nhạy cảm trong môi trường phòng sạch.