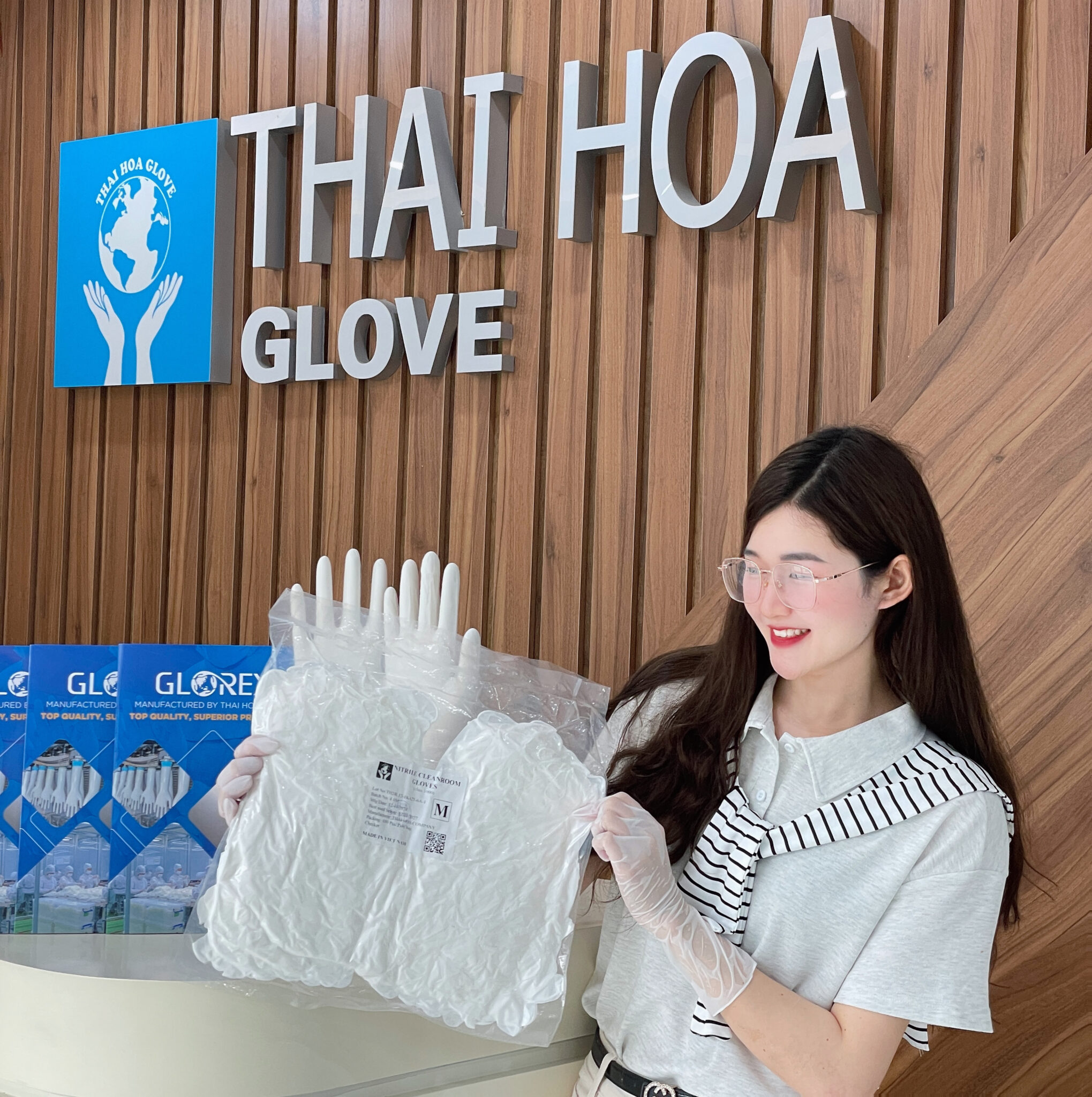
Raw Material Handling Workshop: The Quality Foundation for Cleanroom Gloves
The raw material handling workshop plays a key role in the cleanroom glove manufacturing process. Here, raw materials are received, inspected, prepared and processed meticulously before moving to the next production stages. The quality and careful preparation in this workshop have a direct impact on the quality, cleanliness and performance of the entire cleanroom glove manufacturing process. With strict requirements on the environment and product standards, the raw material handling workshop needs to be strictly designed, operated and controlled.
Receipt and Inspection of Incoming Materials
Process at the Workshop begins with Receiving and Inspecting Raw Materials
The process at the workshop begins with the reception of raw material batches, including the primary polymer nitrile butadiene rubber (NBR) and other synthetic polymers depending on the type of gloves being produced. Each batch of materials must be accompanied by all relevant documents, such as the Certificate of Analysis (CoA) from the supplier, Certificate of Origin (C/O), and other technical documents.
Once the materials are delivered to the workshop’s receiving area, the Quality Control (QC) team performs strict inspection steps as per the established procedures. These inspection steps include: